August 31, 2021
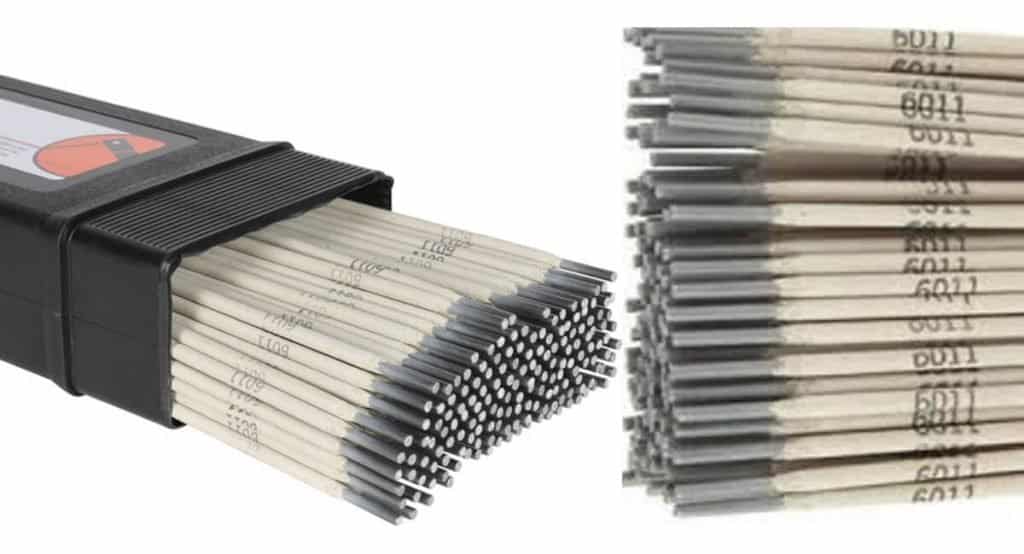
The E6011 “stick” electrode or welding rod is one of the well-known “fast-freeze” electrode types. Being a “fast-freeze” welding rod, the E6011 electrode can be used in all welding positions. Moreover, the flux coating of the E6011 electrode allows for both DCEP and AC power supply.
In order to correctly identify a certain electrode or welding rod, the American Welding Society has devised a means of classifying welding rods. The “E” stands for electrode, the first two or three digits indicates the number of the weld metal’s minimum tensile strength in kilo-pounds per square inch (ksi). The penultimate figure signifies the welding position, and thus, the electrode’s welding characteristics or group. Lastly, the final digit denotes the type or types of current used during the welding process. Hence, in E6011, the 60 means 60 kpi (or 60,000 psi) the first number 1 signifies that the electrode can be used in all welding positions indicating that the weld solidifies quickly and thus, is very applicable for overhead welding. The last number “1” means that it can use either AC current and both DC polarities due to the high cellulose potassium flux coating.
The E6011 electrode is a cellulose electrode as its flux coating contains cellulose. Cellulose is an organic compound that consists of around 30% of the total amount in weight of the electrode coating. In some places, wood powder or paper pulp is added to reduce the cellulose content. The cellulose content in the flux coating of a cellulose electrode like the E6011 is transformed into hydrogen, carbon monoxide and carbon dioxide gas in the arc which, in turn, increases the tensile strength of the welded part. Moreover, the cellulose coating of the E6011 welding rod allows for deeper weld penetration. Furthermore, the E6011’s high cellulose potassium coating allows and helps conduct AC electric current.
E6011 Applications & Uses
The E6011 electrode is an all-purpose welding rod that can be used for repair and fabrication works. It is also applicable for welding large diameter pipelines with wall thickness of less than 12.5 millimeters.
The E6011 welding rod is suitable for welding of mild steels, galvanized steels and certain low alloy steels. The coating of this sturdy steel electrode produces a smooth spray-type arc, forceful enough to achieve deep penetration while leaving a thin layer of easily cleaned up slag. Also, the coating endows the 6011 with very high arc stability, as well as greater deposition efficiency and flexibility, while producing little spatter.
The E6011 has similar qualities to E6010, but the E6011 has the advantage of being able to run on both AC and DC current, making it compatible with small AC as well as DC type of welders. Furthermore, its powerful arc force and quick weld metal solidification make the E6011 an all-position welding rod, suitable for flat, horizontal, vertical or overhead positions.
The combined characteristics of the E6011 make it useful to a wide range of application areas. Due to its profound penetrating ability, it is particularly helpful in welding of greasy and corroded steel as well as for bad groove fit-up welding. It often used for automobile body shops and in welding of farm equipment made of mild steel, as well as in shipbuilding, the construction of bridges, railroad cars, boilers, barges, and the manufacturing of truck frames, pipes, pressure vessels, storage tanks, galvanized steel, and other fabrication processes.
Amperage Settings
Like any other electrodes, the E6011 is available in various diameter sizes from 3/32” to a quarter (¼) of an inch. As the electrode’s diameter size becomes larger, the amperage increases. For example, welding horizontally a ⅛” (3.175mm) diameter rod requires 90 to 140 amps, while welding 3/16” (4.7625mm) diameter rod would require 160 to 195 amps. Moreover, the welding position also dictates another increase in amperage. A 3/16” electrode, for example, would require 160 to 180 amps on vertical welding position and 140 to 180 amps when in overhead welding position. Lastly, it is important to check for the recommended values and settings posted on your welding machines.
6011 Rod Polarity
As you become well-versed in welding, you will understand that arc welding is often performed using direct current with the rod acting as the negative electrode. This way of welding is referred to as DC- or what we often term straight polarity welding. However, in some situations, you will use the rod as your positive electrode, which is aptly termed DC+ or what we call reverse polarity welding.
If you are engaged in welding extremely rusty and dirty stock, you might as well use AC. The thing is, when welding, you should match the rod with its polarity.
Moreover, you should remember that some rods only function with either one or two polarities. The 6011 rods, nevertheless, work well with any type of polarity. Moreover, the 6011 rods will work well with cracker boxes, DC-, or DC+. All you must do is adjust the settings of the welding machine to whatever setup you want to use the 6011 rods. Thus, you don’t need to worry about polarities when using 6011 rods.
Features of E6011 Welding Rod
Like any electrodes, the E6011 has its own benefits and advantages. Here are some of its best qualities:
- The best-known benefit and/or advantage that the E6011 electrode possesses is its ability to operate in all three types of current available from a power source: direct and reverse polarity DC and AC. You can readily switch from one current to another to find what would bring in the best results.
- The E6011 welding rod can also be used to weld unclean and rusty surfaces. There is no need for performing additional tasks of clearing rust and dust.
- The E6011 penetrates deeply into the workpiece. This is due to the digging arcs that the E6011 produces. This penetration ensures larger and deeper weld coverage that results into much larger fused area as well as stronger bond. The E6011 is especially suitable for welding tight-fitting or unbeveled joints. • Being a “fast-freeze” electrode, the E6011 can also be used in any position as the weld readily solidifies, preventing the weld from shifting or flowing.
Electrode 6011 Benefits and Advantages
Like any electrodes, the E6011 has its own benefits and advantages. Here are some of its best qualities:
- The best-known benefit and strength that the E6011 electrode possesses is its ability to operate in all three types of current available from a power source: direct and reverse polarity DC and AC. You can readily switch from one current to another to find what would bring in the best results.
- The E6011 welding rod can also be used to weld unclean and rusty surfaces. There is no need for performing additional tasks of clearing rust and dust.
- The E6011 penetrates deeply into the workpiece. This is due to the digging arcs that the E6011 produces. This penetration ensures larger and more in-depth weld coverage that results in the much larger fused area as well as stronger bond. The E6011 is especially suitable for welding tight-fitting or unbeveled joints.
- Being a “fast-freeze” electrode, the E6011 can also be used in any position as the weld readily solidifies, preventing the weld from shifting or flowing.
- It can penetrate the paint, rust, dirt, and other contaminated surfaces.
Potential Issues with the 6011 Welding Rod
One of the drawbacks of the E6011 is that although it produces flat beads, it does leave ripples and gives a rougher finish, not as aesthetically pleasing as that of 6013, for example.
Another issue that can arise, given enough restraint and metal pollution, is the cracking of the centerline of the welds. This is where all the impurities of the melted base metal and the weld metal gather, as it is the last point to solidify. This is more likely to happen with a large flat fillet weld deposits made in a single segment with the base metal plates positioned at an exact 45-degree angle plane. Therefore, to avoid cracking the weld deposit sequence should be made in segments, and the position angle of the plates should keep less than 45 degrees. Preferably, the position angle should vary within about 10 degrees, so that base of the joint isn’t along the lines of the centerline of the fillet weld.
Some Advice for Vertical Uphill Welding Using the 6011 Rod
If you are a beginner, you may be tempted to use one hand to weld while propping with the other, the same way more experienced welders do. However, keep in mind that the steadier the hand, the better the result. So, find a way to prop and make yourself comfortable.
Apply the whip and pause technique, going about halfway back into the puddle while moving forward, creating an even flow, about one motion segment per second.
85 amperage is an appropriate starting point, producing enough heat for the puddles to flatten out, yet not being so hot as to risk arc blow near the end of the rods.
Should your machine have a dig function, which is beginning to be more common nowadays, set the dig to 50-60. Note that the dig settings vary for different rods. An appropriate dig setting for the E7018 rod, for example, is 30.
How to Store the E6011 Rods?
When storing the E6011 rods, you need to keep them inside their original packaging. In this way, you can prevent damage to these rods due to moisture, although the 6011 rods are not like the 7018 and other rods, which moisture can quickly damage. The 7019 rods, for example, must be stored inside an oven at around 250°F once taken out of their packaging. The 6011 rods, on the other hand, must be kept in a dry place or container and should not be left outside.
One best way to store the 6011 rods is to keep them in an old toolbox made of metal. Then mount it on the wall in a vertical position and affix a light fixture on its top with a 100 W bulb.
When Should You Not Use 6011 Rods?
The E6011 may not be the best rods to use on most occasions. In fact, one of the downsides of using the E6011 is that it leaves ripples and provides a rougher finish compared to other rods like the 6013. So, you end up with a less aesthetically pleasing finish when using 6011 rods.
Moreover, you should refrain from using the 6011 rods when dealing with sheet metal because it is more challenging to operate with sheet metal and quickly burn holes into the sheet metal. It will be best to look for better choices that are designed for thin stock.
Besides, you may find the 6011 hard to control and strike. So, if you are a novice, you might as well use other rods, for you may find it challenging to keep this rod from attaching itself to the bead.
Furthermore, you should refrain from using the 6011 on non-ferrous and stainless steel. If you are working on metals like copper, aluminum, titanium, and stainless steel, for example, it will be best to use a TIG welder equipped with a filler rod consisting of similar metal as your base.
Another drawback of using this welding rod is the centerline cracking of the welds. This cracking usually happens when you create a somewhat wide filler weld using the 6011 rods. To remedy such cracking, you should make the weld deposit sequence in segments, and your plates’ position angle should be lower than 45°.