April 28, 2022
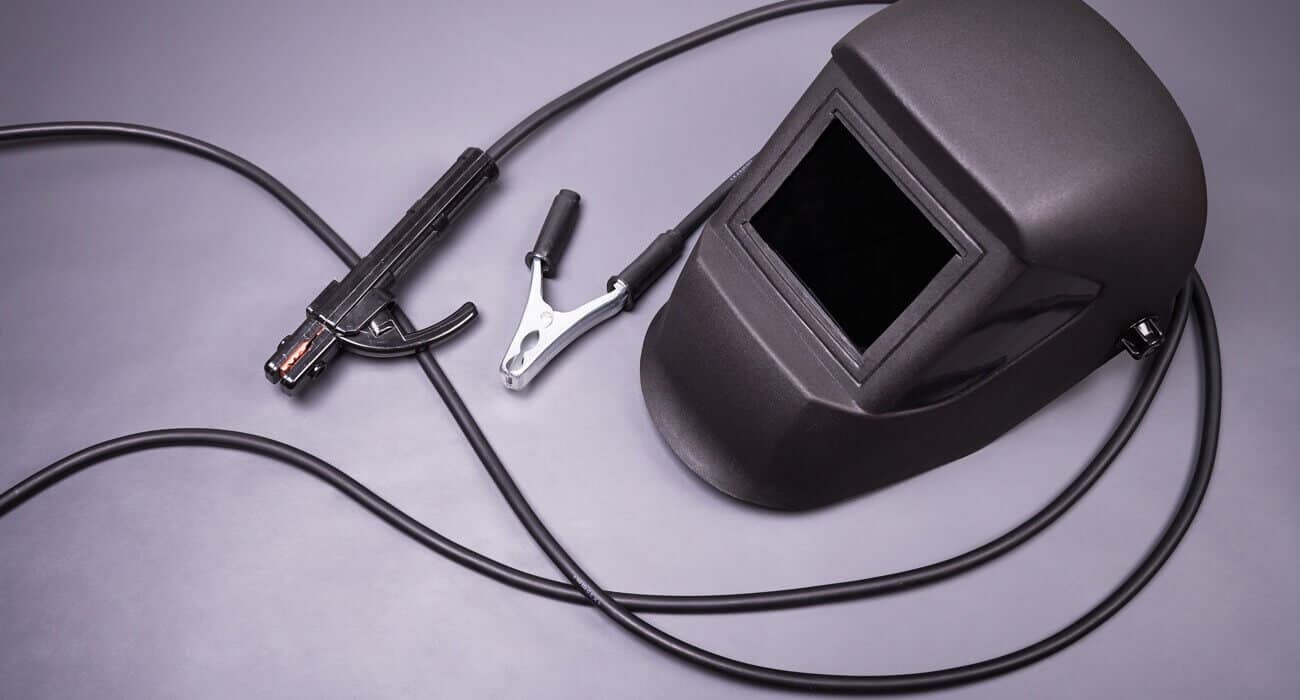
To be able to relay current to the welding electrodes, a welder needs a welding cable. This welding cable serves as the electrical conductor and the pathway of current. The welding cable usually consists of fine strands of copper that are wrapped around by a durable non-conductive jacket. This durable jacket serves as the insulator and is generally made of natural or synthetic rubber. The choice of copper strands for the welding cable is very apropos because copper strands provide more flexibility as compared to other electrically-conducting materials.
The current level is usually measured in amps or amperage. As the level of current increases, the cross-sectional area of the copper strands should likewise increase. This is necessary so that the strands of copper wires can readily accommodate the increased level of current.
The Importance of Having the Right Size of Welding Cable
The size of the welding cable usually depends on the current level that the cable is going to conduct or relay. As mentioned above, as the amperage rises, the diameter also of the welding cable should also increase correspondingly. This is because there would be more strands of copper wires needed to convey the increased level of current. Moreover, the greater the number of copper wire strands, the greater the cable’s level of conductivity would be. If the welding cable, however, is conducting more current than it could, chances are, the cable would overheat and may eventually cause fire.
But how can you determine the proper size of the welding cable? Well, it’s a bit easy. First, you should figure out the length of the welding circuit. This means you should measure the length or path that the electricity would travel to effectively weld. The path should include every possible pathway that the current would pass through, including all those components that you are using when welding. Moreover, you need to figure out the maximum amperage that the circuit would conduct when welding. Once you’ve determined these pieces of information, you can then select the right cable size.
It is important to note that the sizes of welding cables are usually indicated by Gauge. You should also remember that the larger the actual diameter of the cable, the lower the gauge will be. AWG or American Wire Gauge is used to categorize the different electrical cable. The AWG categories show that the smaller the diameter of a cable, the larger its number would be. Hence, gauge sizes—that are larger than one are categorized as zero or 1/0, while two zeros are usually expressed as 2/0 or “Two aught,” and so forth. The typical cable sizes that range between number 4 and number 4/0 are the common cables used for welding.
Factors that You Should Consider about Choosing The Right Welding Cables
If you intend to weld and you’re in need of a welding cable, you should bear in mind several factors before zeroing in on a welding cable. First, you should understand the important role played by the welding cable in the welding process. The welding cable is the one that carries the electrical current used for welding. It also consists of copper strands covered with an insulating jacket. Moreover, it is also designed for absolute conductivity, flexibility, durability, and protection. Hence, when selecting the right welding cable, it is necessary to select the right cable that could easily handle the maximum required output when welding.
To be correct in your selection, you need to bear in mind these following factors:
1) Welding Circuits
When welding, the electrical current that you need to power your welding equipment usually flows from a current source to your welding equipment. The length of the current pathway is called the “welding circuit” or the “total path the current would take to travel.” The welding circuit usually consists of the power source, the electrode cable, the electrode holder, the electrical arc, the work cable, and the work clamp. To figure out the size of the welding cable, you should sum up the total length of the electrode cable together with the work cable.
Once you’re done measuring out the total length of all these cables, including the electrode holder and electrical arc, you can then get the total length of the welding cable circuitry. At this point, it is valuable to note that the welding polarity does not factor well in the act of choosing the cable size. Moreover, the direction of the current flow is a non-factor in determining the size of the cable.
2) Capacity of the Welding Cable
As mentioned above, it is important to know the maximum amount of electrical current that a specific cable is capable of handling safely. This maximum amount is also called “ampacity.” The cross-sectional area of the cable (including all its stranded wires) factors well in determining the ampacity of the cable. However, there are also other factors that determine the ampacity of the cable such as those of the ohm rating, ambient temperature, length, and the temperature ratings of the jacket that insulates the stranded wires. It is also important to note that the shorter the cable is, the more current it can carry.
Most welding cables are often rated at 75°C (167° F) and (194⁰F) or 105°C (221°F). Even if the stranded copper wires can handle the high temperatures that are usually generated by a higher flow of current, there is still a strong likelihood that the insulation that protects the stranded wires would melt. Hence, you must also determine the temperature ratings of the jacket. It is also important to note that welding cables are usually rated at 30°C (86°F) relative to their ambient temperature. If the ambient temperature increases, the cable will likely have a reduced ability to scatter or dissipate heat, and this will surely have a bearing on its ampacity. You should also not pack together several cables, for this may have a reducing effect on their ability to handle heat likewise.
3) Rated Output
When choosing a welding cable, you should also carefully consider the rated power output of the source of power. This rated power output is usually indicated and included in the name of the machine such as in the case of Power Wave® S350 and Flextec™ 650 (650A rated output). The rated power output is the maximum amperage or current level wherein you intend your machine to be used. You should note, however, that some power sources usually produce higher amperage than their indicated rated output at some short intervals.
4) Duty Cycle
The capacity rating of the source of a welding power is called the “duty cycle.” The duty cycle is the percentage of operation within ten minutes of a power source at any given level of current output before it exceeds its specific thermal limit. As a general rule, the duty cycle typically increases as the output level decreases and vice versa. You can find the duty rating on the nameplate of the power source; you can also find it in the operating manual. Lastly, it is important to note that there is a correlation between the welding processes, the intended usage, the operation processes, and the welding power source.
How to Maintain Your Welding Cable in Good Shape
Regular and proper maintenance of your welding cable would surely lead to a longer lifespan for your welding cables. Hence, at the onset, you should ensure that you have purchased the right and the best welding cable for your welding needs. To zero in on the best welding cable.
Cabling Environment
First, you need to know in which environment you are going to use your welding cable. If you intend to use in an environment characterized by vulnerability to abrasion, high temperatures, harmful chemicals, and other hazardous ambiance, you must select a cable that is designed for durability. Moreover, you should also not forget the value of choosing the right cable size.
Avoid Twisting & Kinking The Cable
When using the welding cable, you should ensure that you are careful to avoid any inadvertent damage to your welding cable. Avoid twisting or kinking the welding cable. You should also avoid added tension to the cable and at least keep the cable from being pressed upon or crushed by any heavy object, for it may damage the insulator or jacket of the cable. You should also keep the cable away from anything that could damage the wires like an open flame or hot object. Always see to it likewise that the cable reel is properly adjusted. You should also try to switch the cable ends if one end has been exposed to the harsher environment for a very long time. Lastly, you should follow these the abovementioned tips.
Always Inspect For the Damaged Cable
Wires are inadvertently damaged, and these damages may go unnoticed to you. Hence, if you intend to keep your welding cable in topnotch condition, you should often inspect the full length of the cable for some damages. If there are some small damages, you should try to remedy these damages or make some repairs to avoid being forced to replace your welding cables along the way. You should also take extra effort in removing crushed, or cut wires for these damages may become potentially fatal to you and other people. Moreover, you should always have a spare cable in handy to avoid delay in your work.
Record The Installation & Replacement Date
As every tool or cable has its rate of deterioration, it is wise to keep a record of when you started to use your welding cable and other electrical wirings. If you have a record, you can have a reasonable expectation as to when the cable will reach its wear-and-tear limits or when you are going to replace them. Moreover, you should take note of the time you did some fixing on the cables so that you can have a reasonable assessment of damages if they are recurring. With all these records, you will be prepared for any potential damage or problem with the cable, while at the same time, you can have an honest assessment of the underlying problem. Always remember that your memory will often not serve you right and that anything that is written is always remembered.
Nota Bene:
It is important to note that despite the fact that copper is one of the most excellent conductors at hand, it still posits some degree of resistance to the flow of the current. Hence, you can expect a certain amount of resistance to current while using a stranded copper cable. This certain level of resistance may also cause a certain amount of heating in the cable. For this reason, you should not be alarmed if you feel that the cable is warming up for this is relatively natural even if you have chosen the right cable size.
As long as the cable is correctly sized, you need not worry about overheating cable. But if the cable is undersized, you should worry about it for it may soon overheat and this overheating may be a potential fire hazard. It may also cause the insulator jacket to break and may eventually give you an electrical shock.