June 11, 2021
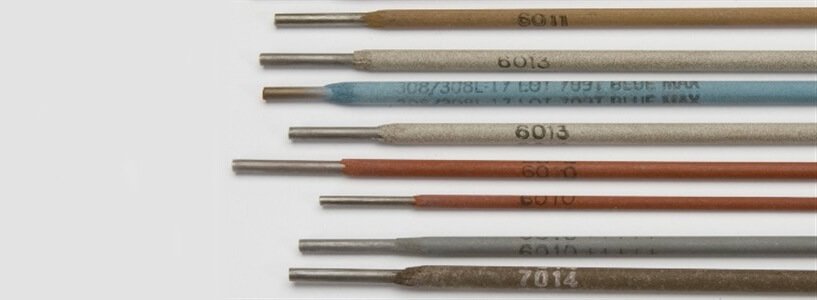
Welding is the process of fusing two pieces of metals (also called workpiece) together. This is accomplished by passing electric current from the welding electrode to the workpiece that creates an electric arc. The electric arc heats and melts the two metals together, which in turn, fuses the two metals together resulting in a stronger bond. The welding machine supplies the electric current which is either in the form of alternating current (AC) or direct current (DC).
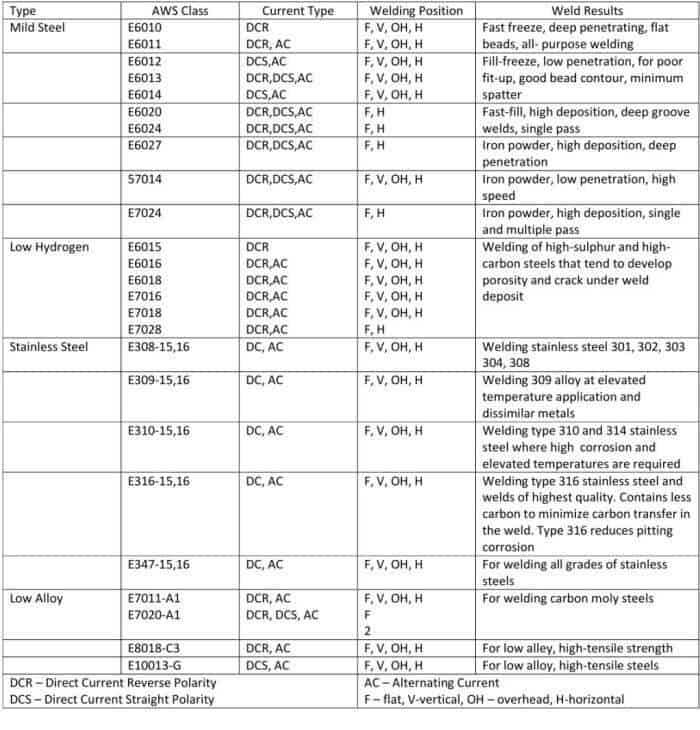
What Is A Welding Rod?
The welding electrode, which is commonly known as “welding rod,” is a piece of flux-coated metal wire that also acts as filler when used in the welding process known as the “shielded metal arc welding” or SMAW. In the SMAW process, also commonly referred to as “stick” welding, the welding rod (a.k.a. “stick” electrodes) melts along with the workpiece, acting as filler. Due to this action, the welding rod is generally categorized as consumable electrodes type.
The welding rod is primarily consisting of a metal wire or rod and its outer flux coating. This metal rod melts when the electric arc is created and becomes part of the weld. This metal rod should be usually similar or identical material to the workpiece. However, there are welding cases that the welding rod and workpiece are of dissimilar materials.
The flux coating is the material that decomposes into a shielding gas during the welding process. The gas shielding protects the weld pool—the molten steel—from being contaminated by the atmospheric gas. Part of these flux coating likewise turns into a kind of plaque known as slag, which protects the weld as it cools.
What’s in the Name?
The American Welding Society (AWS) has devised an alpha-numeric system for naming welding rods. At present, this naming system is arguably the most widely used system to identify a welding rod. This alphanumeric system reveals the designed used and welding characteristics that differentiate each welding rod.
If you are a beginner in the welding industry, you may be confused upon looking at the welding rod classification, for you would readily notice that the welding rod chart have numerical digits. You should not be perplexed with these numbers for these numbers correspond to certain values. If you would take, for example, the 7018 welding rod, you would notice that there are four numerical digits. The first two numbers of 7018 correspond to the tensile strength or the stress-bearing capability of the weld bead. Hence, in the case of 7018 welding rod, the weld bead can withstand 70,000 lbs. Per square inch. For this reason, the higher the first two numbers, the higher the strength of the electrode.
The third digit, on the other hand, refers to the number of positions in which the welding rod can be used. It would be good to remember that there are four primary welding positions, namely, the flat, horizontal, vertical, and overhead positions. A number “1” on the third digit, therefore, basically means that it can be used for all four welding positions.
The last digit, however, refers to the coatings used on the electrodes. Electrodes are usually coated with varying chemicals to protect the joints when welding. These chemical coatings can determine the amount of current that could be applied during the welding process. Moreover, welding power supply varies according to the amount of current needed in the welding process. The power supply can be as simple as a car battery or as sophisticated as the high-frequency inverter that uses IGBT technology and can be controlled by a computer. Hence, the last digit together with the penultimate digit may indicate which type of power supply is appropriate for the welding process—whether it would be AC, DC+ or DC-.
Different Types of Welding Rod Flux Coating Materials
There are different types of materials used as a flux coating. These materials include rutile (TiO₂- titanium dioxide or Titania), calcium fluoride (CaF₂), iron powder, and cellulose. These materials or mixture of these materials and/or other additional materials are used to allow certain types or different types of current to be used during the welding process. For example, specific electrodes use reverse polarity or DC+ current for welding; another would use direct polarity DC- current; some electrodes, however, could use both DC+ or DC- in lieu of each. But the majority of electrodes can also use alternating current (AC) instead of the already mentioned DC types. Moreover, welding rods are divided into three groups in accordance with welding characteristics. These groups are the following:
• Fast-Fill Welding Rods – The “fast-fill” welding rods are designed to melt allowing maximized welding speed quickly. These welding rods are excellent only for flat, horizontal position welding jobs. “Fast-fill” are heavily coated electrodes that produce a lot of slags on top of the weld.
• “Fast-Freeze” Welding Rods – The “fast-freeze” welding rods are quick to solidify and allow for all welding position. During the welding process, the weld pool readily solidifies, and this quick solidification prevents it from shifting. The fast-freeze are also commonly associated with reverse polarity (DC+) but can also operate with AC power. Fast-freeze welding rods produce flat beads and minimal slag.
• “Fill-Freeze” Welding Rods – The “fill-freeze” also known as “fast-follow” electrodes are general-purpose welding rods that produce wide coverage of slags. “Fill-freeze” are commonly known as straight polarity (DC-) electrodes, but they can also use AC or alternating current.
A group of electrodes known as the “low-hydrogen” welding rods is also recognized by welding pedagogues as the fourth group of welding rods. These low-hydrogen welding rods are designed to weld high-carbon or high-sulfur steel. These welding rods reduce hydrogen absorption by producing X-ray quality deposits on the weld.
Understanding the Commonly Used Welding Rods
There are many types of welding rods, and it would be good to know what each of these welding rods has to offer:
1) 6013 Welding Rod
The 6013 welding rod is capable of withstanding 60,000 lbs. of stress per square inch. Since its third digit is 1, it means that it can be used for all welding positions. Although the 6013 has a lesser tensile strength than the 7018 welding rod, it is still pretty strong and can complete most welding projects. The last two digits of 6013 also indicate that its electrode has a high titanium-potassium coating, and for this reason, it is compatible with almost all types of power supplies and currents. The use, therefore, of 6013 provides pro welders with more versatility for they can alternately utilize this welding rod using different types of currents.
Sometimes beginners in the welding process are first introduced to other types of welding rods like those of the 6010 and 7018 welding rods, and for this reason, they fail to see the advantages concomitant with the use of 6013. But once they begin to use the 6013, they immediately discover its advantages. They also learn that 6013 can be easily paired with small and entry-level welding machines.
The good thing about the 6013 welding rod is that it is ideal for smaller welding jobs because it allows for medium-range penetration on thinner metal sheets. The downside of using 6013 is that it produces more spatter than that of the 7018. However, you can readily remove these slags as quickly as they appear. Hence, the end-result of using 6013 is surely clean and optically appealing.
2) 7018 Welding Rod
As explained above, the 7018 welding rod is capable of withstanding the pressure of 70,000 pounds per cubic square inch. The third digit also indicates that it is an all-position rod. Moreover, the last two digits of this welding rod also tell us that the electrode is coated with iron powder with low hydrogen coating. Hence, both AC and DC+ currents can be used to operate this welding rod.
The 7018 welding rod is sometimes referred to as low-high rod. The reason for this is that the low hydrogen content of its electrodes generally produces smooth, yet very strong welds. The downside, however, of using 7018 welding rods is that these rods must be kept in moisture-free storage because moisture can radically reduce the lifespan of these rods. Moreover, these rods should not come in contact with water for water can also diminish its lifespan. For this reason, you need to store the 7018 rods in moisture-free storage like that of that of an oven of around 250°F, especially, if you would not use them for several hours. Some pro welders usually have a purpose-built oven designed for storing these types of welding rods. However, if you don’t have enough budget for this type of oven, you simply can create an improvised oven to keep your 7018 rods free of moisture.
3) 6011 Welding Rod
If you have already used the 6010 and 6011 welding rods, you would readily notice that there is a semblance between these two types of welding rods. By simply considering their names, you would readily realize that both welding rods can withstand 60,000 pounds of pressure. Moreover, they are applicable for all types of welding positions. The differentiating factor that sets these two types of welding rods apart lies in the consideration of the last two digits of these two types of welding rods. The 6011 has very high coating level of cellulose potassium. Hence, it can operate using AC and DC+ currents. This implies too that 6011 is usable with any type of welding machines. You can also use it if you are operating bigger types of welding machines. Moreover, you can achieve deep welding penetration with this type of welding rod, and you can also readily use it with dirty and corroded metals because of its deep penetration capability. For this reason, it is ideal for repair welding works.
The downside, however, of the use of this type of rod is that it produces a bit of slag which is more difficult to remove than the slags produced by other welding rods. Hence, if you don’t have enough patience and time for removing unwanted slag, you should instead opt for other types of welding rods.
4) 6010 Welding Rod
The 6010 welding rod is ideal for deep penetration and welding on corroded and dirty metals; hence it is ideal for patchworks and repair jobs. The 6010 also has the coating of high cellulose sodium. This implies that you can only use it with DC+ current. Hence, it is pretty much useless if your power supply is AC. Compared to 6011, 6010 can perform more smoothly than that of the 6011, and produce easier-to-remove slag.
However, despite the easy availability of 6010 welding rod, it is in actuality very difficult to handle and use. The difficulty lies in the fact that it’s electrode is not easy to grip since it produces a highly tight arc. Hence, it is necessary to learn how to restrain and control the tight arc of 6010 before you can gain mastery of its use.