June 11, 2021
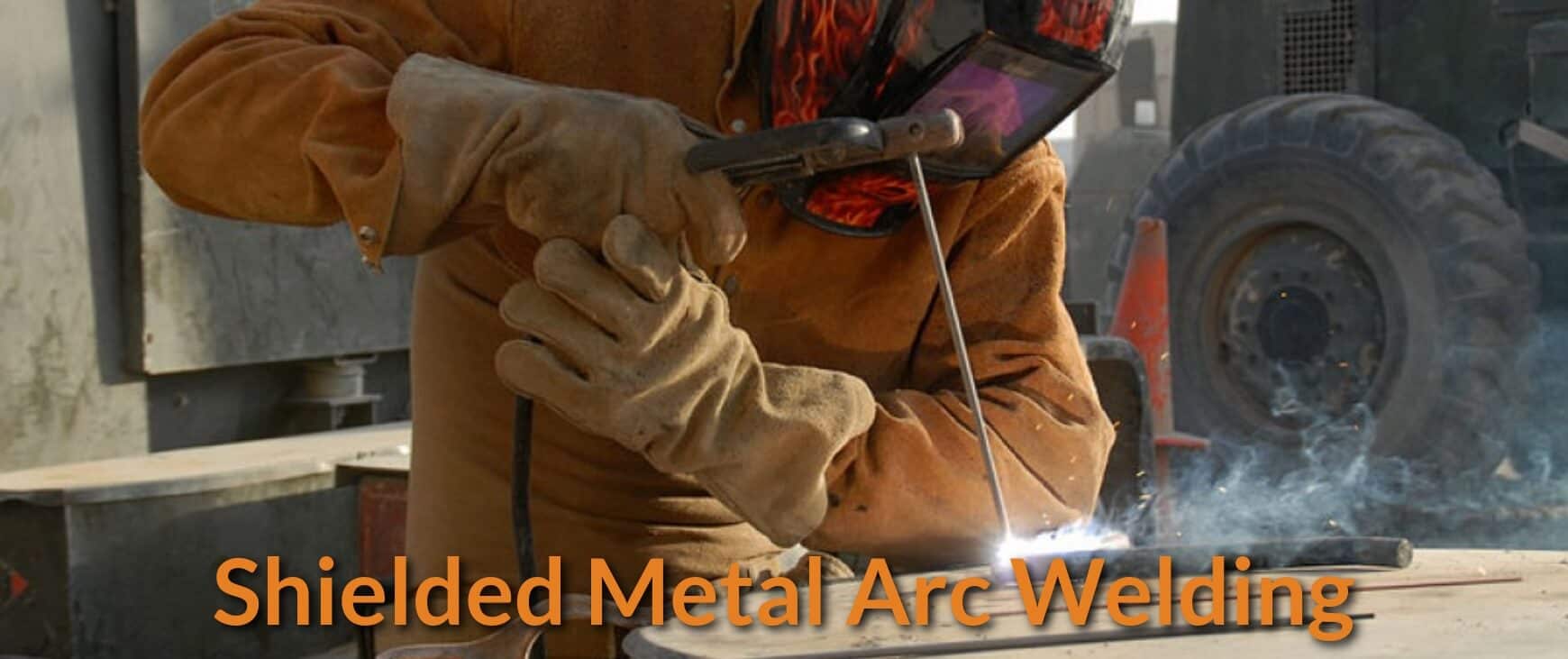
Shielded metal arc welding (SMAW) is arguably the most popular type of arc welding process that is presently utilized. SMAW is known by many other names such as manual metal arc welding (MMA or MMAW), or flux shielded arc welding (FSAW). Moreover, SMAW is more commonly known as “stick” welding due to its use of a stick-like, consumable welding rod.
Understanding SMAW/Stick Welding
SMAW or shielded metal arc welding is a welding process that uses fusion to join two pieces of metals together. Fusion is obtained by melting the materials to be joined into weld pool by employing an electric arc between the electrode and the workpiece. During the welding process, the molten metal from the electrode called “filler” travels via the electrical arc and is deposited into the molten weld pool. This molten pool is protected from the atmospheric nitrides and oxides by the gases that are released from the vaporization of the flux coating of the electrode. Flux residue or slag is also formed on top of the weld pool to protect the weld pool (from atmospheric effects) as it cools and solidifies.
SMAW or stick welding is one of the oldest forms of arc welding process and is said to be the simplest and most affordable welding process that is in use today. This is due to the simplicity, ruggedness, availability, and affordability of stick welding equipment.
The Popularity of SMAW/Stick Welding
Just because of the versatility of the process and the simplicity, availability, and portability of the welding equipment and operation, SMAW remains to be one of the world’s leading processes in terms of arc welding. SMAW dominates other forms of welding processes in many applications like maintenance and repair. Despite the FCAW or flux-cored arc welding’s growing popularity, SMAW continues to be dominant when it comes to construction, industrial fabrication, erection of heavy steel structures, and equipment repair applications.
Another advantage of SMAW is that it can be used outdoors, even during rainy or windy condition. SMAW also does not rely on external shielding gas, and it works well even on rusty and dirty metals. Moreover, in addition to its common applications on welding iron and steel, SMAW can also be used to weld carbon steel, cast iron, and alloy steel. SMAW process can likewise be used to weld nickel, copper or their alloys, and in rare cases, even aluminum.
SMAW/Stick Welding Operation
Stick welding is a process that requires substantial skill on the part of the welder: yet, the SMAW procedure seems to be very simple to perform. To create an electric arc in SMAW, the electrode must be brought into contact with the workpiece, and when ignited, the electrode is slightly pulled back. Upon ignition, the electrode must be held with its tip slightly inclined and at a lower angle to the workpiece, allowing the weld pool to flow. If the electrode is held perpendicular to the workpiece, the electrode tip will likely get stuck on the workpiece. As the electrode core melts, droplets of molten metal are passed to the workpiece while the flux coating disintegrates and vaporizes to form a protective atmosphere over the weld pool. The flux likewise provides molten slag which covers the filler metal on the weld pool and protects the weld pool from contamination as it solidifies.
When welding, it’s important to use metals that conform to AISI-SAE 1015 to 1025 requirements as these metals have low silica and sulfur content and work well with SMAW welding process.
SMAW/Stick Welding Equipment
SMAW welding equipment includes a constant current power supply source, electrode holder and cable, a ground cable and clamp that need to be connected to the workpiece, and a consumable electrode or welding rod. This power supply, otherwise known as “welding machine,” basically comprises of a step-down transformer and a rectifier. The rectifier converts AC (alternating current) to DC current. On the other hand, the transformer reduces the voltage while it increases the electrical current.
SMAW Power Source
SMAW requires a constant current output to energize the electrode and create the electric arc. SMAW operates on either DC or AC power supply. SMAW also uses the constant current output to ensure that both current and the resultant heat remain constant even if the voltage fluctuates or the arc distance changes due to manual control. However, with SMAW, the current is not always maintained at absolutely constant level; moreover, with SMAW, skilled welders can perform varying arc length resulting in complicated welds that can cause minor current fluctuations.
In SMAW or stick welding process using DC power supply, two welding types are depending on polarity. These two welding types are the DCEN and the DCEP. DCEN or direct current with the negatively-charged electrode is used to create shallow weld as the heat buildup is concentrated at the electrode resulting in a fast electrode melt rate. In DCEP or direct current with the positively-charged electrode, the polarity is usually reversed, and the heat buildup is concentrated at the workpiece, resulting in increased weld penetration. Furthermore, it is the alternating current or AC that can provide the best balance between weld penetration and electrode melt rate.
The Electrode
SMAW uses consumable electrode or welding rod. This electrode is typically made of a metal core wire and a coarse flux coating. The flux gives off protective gas or gases over the weld pool as it vaporizes to prevent weld contamination. It also deoxidizes the weld, forming itself into a weld-protecting slag over the weld pool. The flux likewise helps to improve the stability of the electric arc and the weld quality.
The choosing of the right electrode depends on certain conditions such as the type of material to be welded, the desired weld properties, and the welding position. Electrodes can be categorized into three groups—fast-fill, fast-freeze, and fill-freeze electrodes.
- “Fast-fill” welding rods like E6010 and E6011 have quick-melting property resulting in high disposition rates.
- “Fast-freeze” rods like E7024 provide a filler material that solidifies rapidly, preventing the weld pool to shift, and thus, allowing for more difficult welding positions such as that of the overhead welding position.
- “Fill-freeze” or “fast-follow” electrode (example E6012, E6013, E7014) is a cross between the abovementioned two types. “Fill-freeze” electrode has both quick-melting and fairly-fast solidifying properties.
- Electrode coatings or flux comes in four main varieties that include rutile, cellulose, iron powder, and the basic electrode.
- Rutile electrode contains a significant amount (25-45%) of titanium oxide (TiO2) or rutile in its coating and is used for general purposes with good welding qualities. Rutile rod is suitable for all welding positions and can be used with AC or DC power source.
- Cellulose-coated electrode contains a high amount of cellulose in its coating that provides deep penetrating arc and high welding speeds.
- Metal powder welding rod, as its name implies, contains additional metal powder on its coating to promote increased welding current up to the maximum permissible level.
- Basic electrode contains a high quantity of either calcium fluoride (CaF2/ fluorspar) or calcium carbonate (limestone) in its coating and is the primary coating for “fast-freeze” welding rods.
To facilitate the identification of these different electrode types. The American Welding Society formulated a nomenclature (with four to five digits) for electrodes, stating the tensile strength of the weld metal in ksi (thousand pounds per square inch), positions (e.g., 0—unspecified, 1—all positions, 2—flat and horizontal positions only), and with the last two digits specifying the welding current and electrode coating. For example, the “fill-freeze” E6012 welding rod has a minimum tensile strength of 60 ksi, and uses DCEN, DCEP, and AC currents, and is coated with rutile sodium.
Welding Current Level
The size of the electrode determines the welding current level. However, manufacturers usually recommend the electrode’s current level as well as the electrode’s normal operating range. But as a rule of thumb, an electrode requires about 40 amperes (A) per millimeter of its diameter. To select the suitable current level, you should multiply the electrode’s diameter by 40A to establish the appropriate current level. Hence, for a 4mm diameter electrode, the preferred current level would be 160A, while the acceptable operating range is 140 to 180A.
SMAW Weld Quality
Quality issues can arise from the SMAW welding process. These issues can include weld spatter, poor fusion, shallow penetration, porosity, and cracking. While spatter does not affect the mechanical integrity of the weld, spatter does, however, degrade the appearance of the weld, thus necessitating additional work. Spatter can be caused by a condition known as the arc blow. Arc blow is associated with direct current and happens when the electric arc is deflected by magnetic forces away from the weld pool. This is either due to low voltage or high amperage. Moreover, arc blow can also cause porosity. Porosity is primarily caused by trapped gas in the weld as the metal solidifies, leaving a weak weld. This defect is not visually detectable, and necessary tests have to be performed to detect this defect.
What Made The Poor/Bad Quality SMAW Weld?
Poor fusion is another detrimental defect that arises when using SMAW procedure. This readily visible defect is often caused by the low-voltage contaminated workpiece, or via the use of the wrong electrode. Another SMAW welding defect is that of the shallow penetration. Shallow penetration is caused either by fast travel time and low amperage or by using too large an electrode.
Poor fusion, porosity, and shallow penetration can lead to cracking. Similarly, weld weakening issues like porosity, poor fusion, and shallow penetration can also lead to cracking. However, all these defects can only be attributed to human errors and can only be due to insufficient welding skill.
Safety and Protection
As with any fabrication or any other construction job that employ arc welding, safety and protection are of paramount importance. It is imperative that when working with arc welding, you should wear your protective gears all the time. SMAW welding can be hazardous to your health if you ignore and do not follow proper safety precautionary measures. Working with an open electric arc with its accompanying heat can readily result in skin burns. Moreover, there is always the potential danger of being electrocuted while welding and injury due to electrocution could be life-threatening. Welders are therefore advised to wear heavy leather gloves and long-sleeved jacket when performing welding tasks.
It is likewise imperative for welders to wear welding helmets with the dark faceplate for the intense light produced by the electric arc can readily damage the retina and cornea of the welders’ eyes. Moreover, the work area should be shielded with welding curtains to protect other workers from the intense glare of the electric arc. Furthermore, it is likewise advisable to perform SMAW welding in an open or well-ventilated area to prevent smoke buildup and to reduce the risk of inhaling harmful gases produced during the welding process.